What is machine vision anyway?! Anyone with a little knowledge of this can define it as the automatic extraction of data from digital images. Although this is a bit explanatory, most of you will still ask what does that mean?
Well, the fact is that these machine vision systems are used in a typical manufacturing line that has a steady flow of objects that is quick for any human and its eyes. If you want to track your products on the line and check them for potential faults you will need a camera or an optical system pointed to that line. The next thing you need is proper lighting of the line for the camera to see what it needs to see.
What those cameras do on that manufacturing line is capture images and analyzes them against the defined set of criteria and determine if your product is up to code or not. You also have to know that there are several different production lines and as many, if not more, different vision systems made to oversee them.
The reason for the usage of these machine vision systems is plain and simple – it is faster more consistent and works for longer periods. All of this, by a long shot, beats a real person doing the same job and this is why big manufacturers opt for them. If you want one or more of these for your business and if you want reliability and consistency alongside speed then visit Softengi and see what you can find there.
If you are wondering how to build one yourself you will need huge technical know-how, knowledge of programming and a bunch of other things that go with that. Although it seems like a rather simple task of putting everything in place it is not. It isn’t as straightforward as slapping a high-quality camera and making it snap a bunch of pictures and call it a day.
There are a bunch of unknowns and a great deal of fiddling around to make everything work as intended. You need software that can recognize what that camera has captured from the line and you need something coded into that software that will make it separate bad products or defective ones from good.
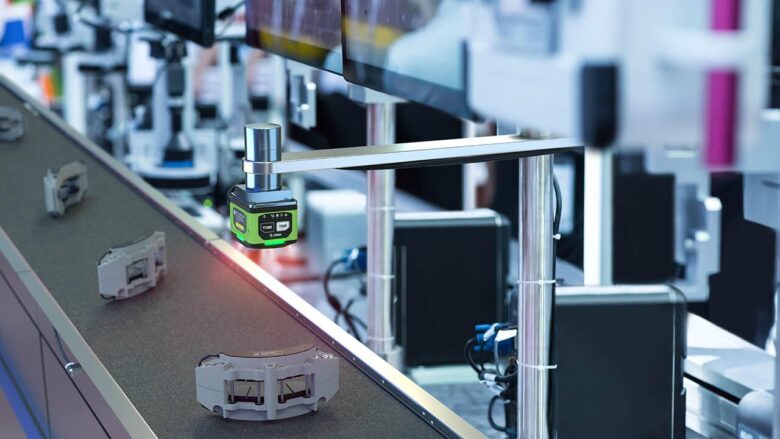
This is truly a task for those that know what they are doing. The best thing that we can advise you is to go ahead and get yourself one of those cameras alongside the required software and have professionals assemble and track everything for you before you put it to use. This way you will make sure that your assembly line runs perfect and that the product that makes it to the end is spot on and the way you attended it to be.
As far as these machine vision systems go, they have come a long way from what they initially were. They are now used in many industries for many valuable processes in manufacturing, primarily. As far as its common applications, you can use these for measurements, counting, location and decoding purposes.
Since its beginning, machine vision has been widely used for measurement and this means a truly automated measurement by the machine. Those measurements are then taken to check against specified tolerances and based on the results your product is deemed as good or flawed. One thing that you will all recognize is the usage of these machines when measuring gaps in spark plugs.
Most of you know that depending on the vehicle and usage this gap has to be of a certain width or your vehicle won’t run as intended. Thanks to machine production and machine vision now you can quickly and easily dispatch those plugs that aren’t up to spec with the tolerances you gave the machine as reference.
Counting is another typical machine vision application and there are a few tasks that fall under this category. Counting means that your camera will look for some parts or certain features that need to be on that part. This will allow you to have an insight in every detail regarding that part and locate if anything is missing or not up to the standards you have coded in. it can also be programmed to look for the absence or presence of certain things on the line and inform you instantly to make adjustments needed.
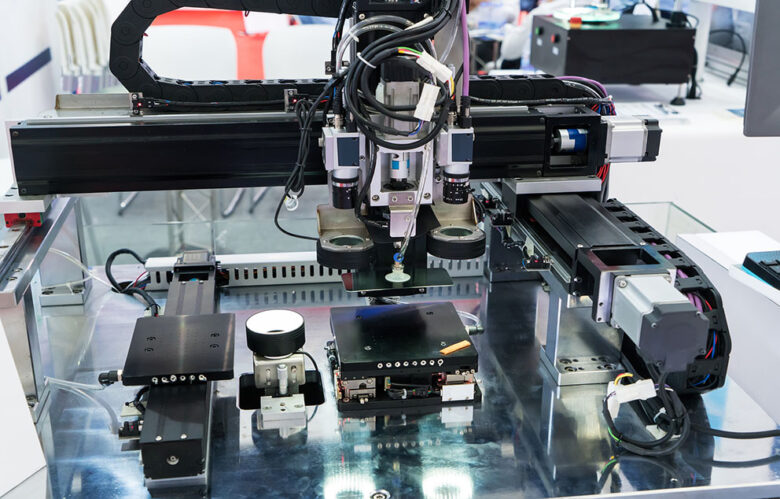
Location in machine vision systems means that your camera will report you on the position and orientation of a part of a product as a whole. This is also useful when you have products that need to be up to a certain standard or when they need to fall into certain tolerances to ensure smooth operation. Some things need to have correct angles to be properly assembled elsewhere.
Decoding is the last application and it refers to the decoding of 1D or 2D symbiology’s like linear barcodes or data matrix codes like QR codes respectfully. Decoding is typically used to record information as historical data that will serve you as a record for parts that have gone through a certain process. This allows you tracking of certain parts through the entire process and utilize that data to take action if needed. This also allows you to look at that data, sort it, validate it and store it or act upon it like we already mentioned.
As you could see machine vision is always the answer when it comes to these things and for the reasons we already mentioned. Higher production, more demand, bigger capacities ask for speed, consistency and to operate longer than any human possible. Machines are slowly but surely taking over certain jobs that were previously deemed as humanly possible and for a good reason. This way you make sure that your products are up to all standards possible, that they will not cause harm to anyone and that your business is safe from issues from the past.
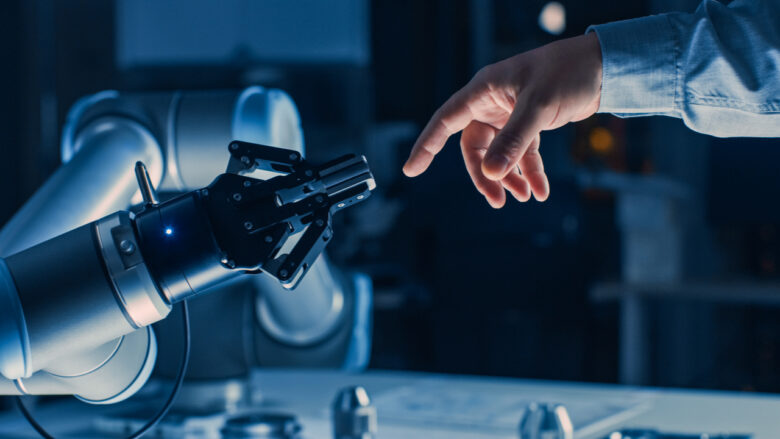
Human errors are there and they are constant and normal. You probably heard this saying a million times “we make mistakes, we are only humans” and it is normal, but when it comes to business, brand name and market shares you need to be as productive as possible, with little to no errors in your products and you have to achieve quality better than anyone else. You will do these things only by enhancing your lines with machines and with machine vision systems that will overlook everything.